BUILDING AUTOMATION SERVICES NEW ZEALAND
PROJECT: HVAC LOAD SHEDDING
CLIENT: PF OLSEN ROTORUA
CHALLENGE:
To meet current building compliance in New Zealand, Renegade Electrics was tasked with designing and implementing a system for safely switching on/off 64 newly installed air conditioning units and 8 ventilation fans in the main HQ building's four wings during fire alarm activation. This building automation solution aimed to restrict passive airflow to prevent fueling/spreading fires.
​

PLC HVAC panel displaying current state
THE TECHNOLOGY:
We utilized four Schneider Zelio SR3B101BD PLC modules with Modbus network cards to provide the automation and communication of the HVAC contactors.
​
As building automation specialists, we leveraged the Ethernet networking capabilities of these controllers for a seamless installation process, eliminating the need for extensive cabling. Utilizing Modbus TCP/IP communication protocol and enabling port forwarding, we ensured remote access over the World Wide Web, facilitating efficient and cost-effective control solutions.
​
We utilized a Schneider HMISTU-655 HMI (Human Machine Interface) to enable end user control, monitoring and trending for on/off times and enclosure temperatures. The end user or technician can access and interact with this information either locally on the site panel or remotely off-site via a smart phone or tablet.

Pre-assembly of the four satellite HVAC control panels prior to installation in the field..

PLC controlled HVAC panels installed.
THE SOLUTION:
We quickly identified that it would also be possible to provide the additional benefits of providing independent load transitioning on the sites submains distribution boards since they were already hardwired through dedicated contactors in addition to the automation for the HVAC equipment (Heating/Ventilation/Air Conditioning) to maximize energy savings and equipment longevity for out of hours non use, and to protect it from unstable power supplies upon re-energisation.
For the HVAC automation, four satellite PLC controlled contactor panels were designed, assembled, and installed and interconnected to each of the adjacent HVAC panels and individually networked back over the local ethernet network to a master HMI user interface. A single fire alarm trigger input or alarm panel armed/disarmed input to the master controller will subsequently cycle off/on all four of the HVAC controllers via the local ethernet communication network to meet the customers requirements. Additional temperature monitoring and control was implemented into each HVAC controller enclosure to ensure no risk of fire/equipment damage should prolonged usage occur.
​
For the load transitioning control a dedicated plc controller was hard wired to the main distribution point, and programmed to switch on each distribution board in a time based sequence following the presence of a stable supply for two minutes. This plc controller was also networked back to the master HMI panel for monitoring and control.

HMI panel displaying partial way through HVAC cycle (Green is On - Orange is Off)

HMI panel displaying enclosure temperatures.
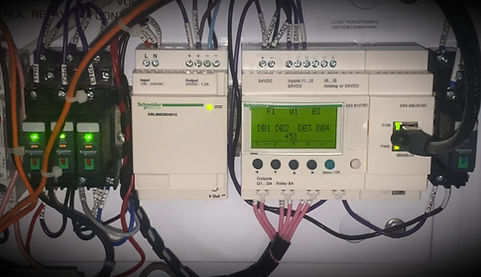
This is the sites load transitioning plc controller to reinstate power to each of the sites five distribution boards and the master HVAC controller.
​
Reinstatement of each DB progressively occurs on minute by minute time based sequence following a power outage return/stabilisation to normal conditions for two 2 minutes.
ADVANCED FEATURES:
Temperature protective control is implemented to ensure each enclosure does not overheat. A thermistor constantly monitors internal temperatures and will cycle of the stages of for that individual controller if the temperature reaches in excess of 40oC. The controller will remain off until the temperature is within range, and then cycle the stages back on. The HMI is programmed to show logging trends, events and alarms. Panel over temperature conditions are an unlikely scenario as the enclosure has panel ventilation and the trending clearly demonstrated a consistent temperature range between 22oC - 37oC.
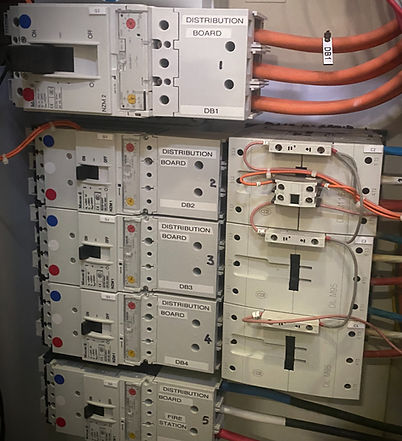
Existing distribution boards with original inline contactors for DB2, DB3 and DB4.